Bi-Fuel Conversions
Until relatively recently, diesel backup generators were really the only practical option for emergency power, although the growing focus on using cleaner energy and sustainability is one of the reasons why more customers are choosing bi-fuel conversions. The fuel can be gas or diesel, although our gas-powered generators are used mainly for combined heat and power (CHP) installations.
Bi-fuel (Dual Fuel) helps you economise on cost by switching between different fuels. We can install new bi-fuel generators or convert your existing asset.
APE’s simple bi-fuel (dual fuel) conversion modifies your original diesel engine so that it uses natural gas as the main fuel – substantially reducing operating costs. It works by introducing gas to the engine via various technologies and then electronically controlling flow dependent on engine speed and output.
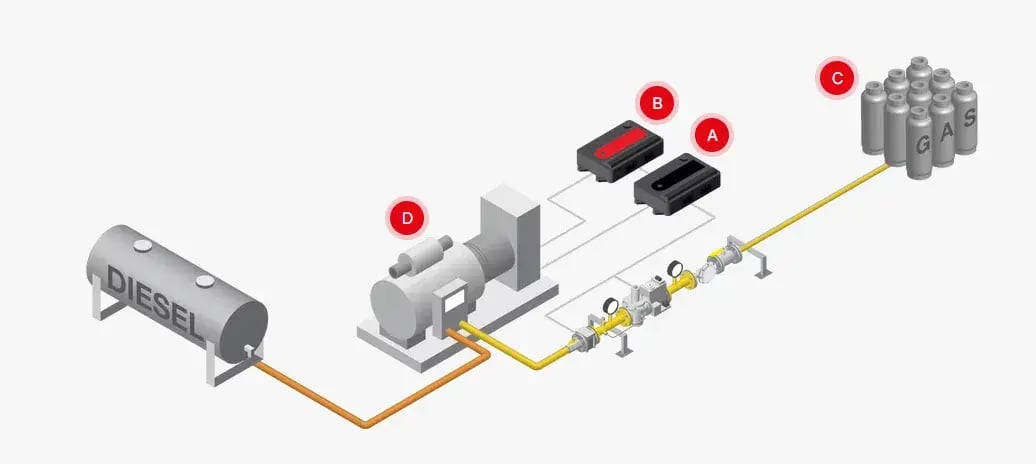
Bi-fuel (dual fuel) conversion requires virtually no engine modification and brings double benefits in every application:
Affordable diesel engines combined with inexpensive natural gas
Economic solution for slow-speed, middle-speed and high-speed engines
Flexible use of fuel
Guaranteed power output
Efficient and safe operation with lower emissions
Longer engine life and reduced maintenance costs makes it the perfect investment
Benefits:
Substantial savings on operation costs
Lower emissions
Slow and Middle Speed Conversions
Practically no engine modification required
Longer engine life span
Non-derated output power
High speed engines - central gas/air mixer (fumigation)
Prolonged service and maintenance intervals
Slow and middle speed engines - individual gas-valve technology
Possibility of original diesel operation at any time
Types of Bi-Fuel Conversions
High Speed Conversions
Substantial savings on operation costs
Practically no engine modification required
Non-derated output power
Possibility of original diesel operation at any time
Lower emissions
Longer engine life span
Prolonged service and maintenance intervals
Types of Bi-Fuel Conversions
Slow and Middle Speed Conversions
High speed engines - central gas/air mixer (fumigation)
Slow and middle speed engines - individual gas-valve technology
High Speed Conversions
Solutions Available For:
High Speed Conversions - central gas/air mixer (fumigation)
Gas is mixed with air by a common mixer installed before the turbocharger(s). Gas flow is controlled by a throttle valve, which is electronically operated by the ComAp control system InteliDrive BF according to the required engine output and speed.
In order to avoid knocking of the engine, ComAp knocking detector/controller DENOX is installed, enabling engine operation at the most efficient gas/diesel ratio.
System for conversion of industrial diesel engines to bi–fuel operation by substitution of typically 50–80% natural gas for diesel.
- Suitable for all High Speed Engines, 1200–1800 RPM
- No reduction of engine power or efficiency
- Smooth transition between diesel and bi–fuel operations at any time
- Gas and air are blended behind air filter before turbocharger by central mixer
- State of the art electronics maximizes the amount of injected gas while keeping all engine parameters within limits specified by the engine manufacturer
- No modifications of internal engine components are required
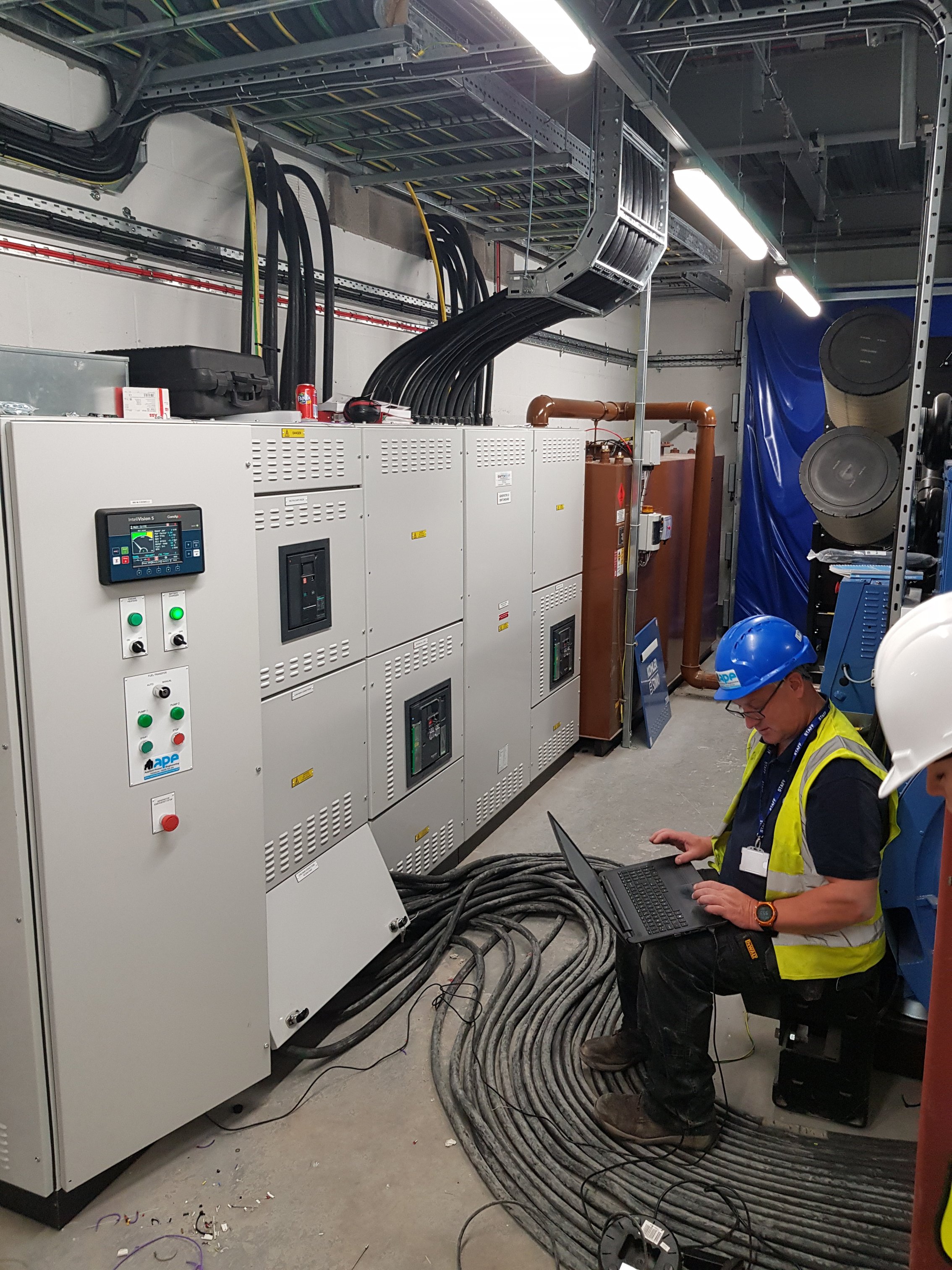
Benefits:
Completely automatic system
Cheaper electricity production
Non–derated output power
The same response to load steps
The amount of gas is maximised as much as possible under varying conditions at any time
High stability and increased protection of the engine
Lower emissions
Possibility of pure diesel operation maintained
Prolonged service intervals
Turn-key solution
Easy operation
- Completely automatic system
- Cheaper electricity production
- Non–derated output power
- The same response to load steps
- The amount of gas is maximised as much as possible under varying conditions at any time
High stability and increased protection of the engine
Lower emissions
Possibility of pure diesel operation maintained
Prolonged service intervals
Turn-key solution
Easy operation
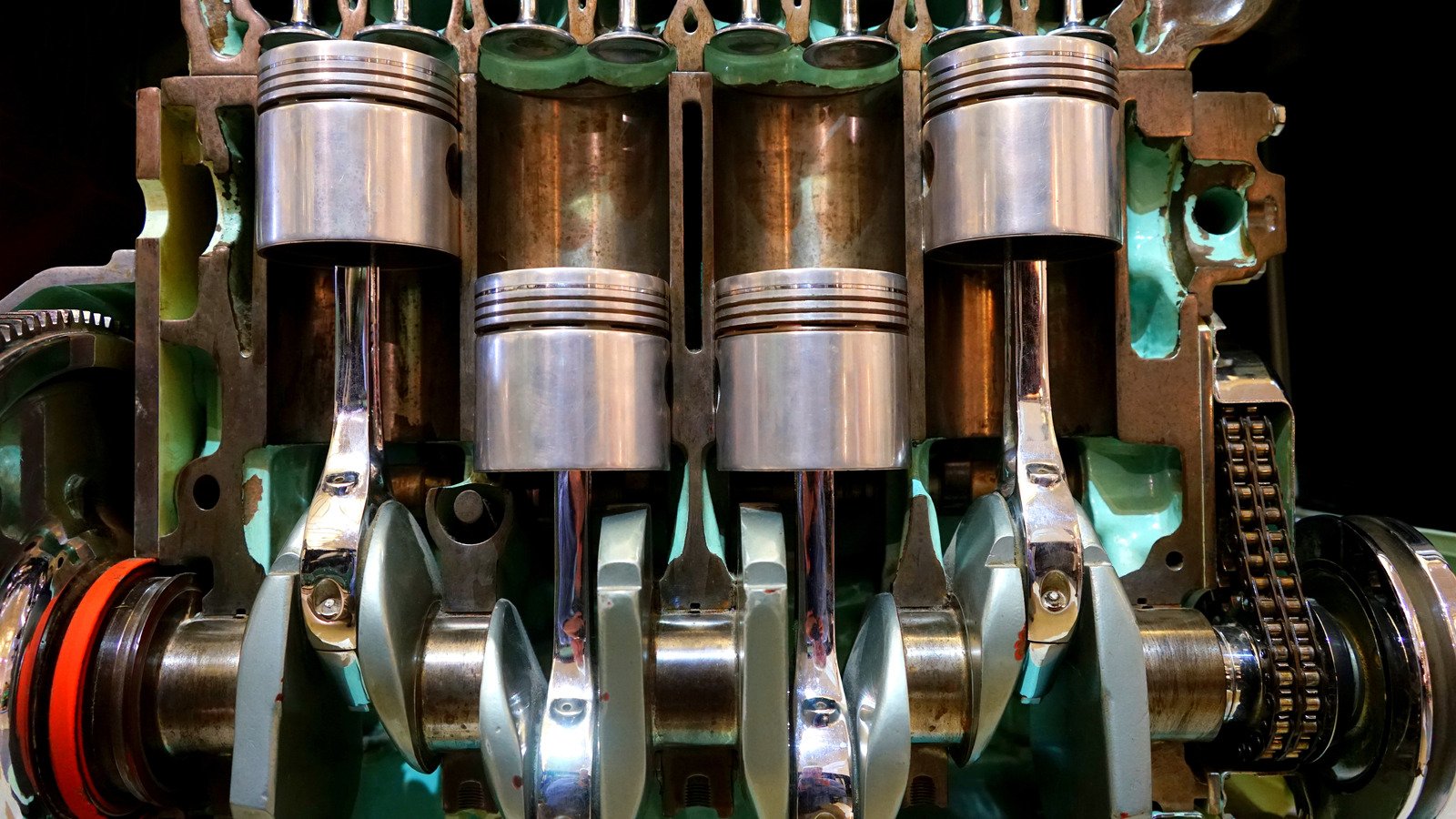
Typical Convertable Engines
High-speed (1200 – 1800 rpm)
Elemental of the System
- Air / gas mixer(s)
- Gas throttle valve with actuator
- ComAp bi-fuel controller/governor InteliDrive BF
- ComAp knocking detector/controller DENOX2/DENOX20
- Sensors (acoustic, pressure, temperature, etc.)
- Gas train (gas manifold, gas governor, double closing valve, filter, ball valve etc.)
Slow and Middle Speed Conversions - Individual gas-valve technology
This works by gas being injected into the cylinder inlet manifold by individual gas electromagnetic valves installed as close to the suction valves as possible. The electromagnetic valves are separately timed and controlled by the ComAp injection control unit INCON.
This system interrupts the gas supply to the cylinder during the long overlap of the suction and exhaust valves (typical for slow-speed and medium-speed engines – while the valve overlap cylinder scavenging is performed). This avoids substantial gas losses and prevents dangerous gas flow to the exhaust manifold.
System for conversion of industrial diesel engines to bi–fuel operation by substitution of typically 60–90% natural gas for diesel or HFO.
- Suitable for engines with speed below 1000 RPM and output above 500 kW
- No reduction of engine power or efficiency
- Smooth transition between diesel and bi–fuel modes at any time
- Gas is injected directly before intake valve by high speed electromagnetic valves, one valve per cylinder
- No modification of internal engine components is required
- Automatic equalization of exhaust gas temperatures from individual cylinders
Benefits:
Extremely efficient operation – only very small percentage of diesel is necessary
Cheaper electricity production
Non-derated output power
The same response to load steps
High stability and increased protection of the engine
Lower emissions
Possibility of pure diesel operation maintained
Prolonged service intervals
Individual approach
Turn-key solution
Easy operation
Extremely efficient operation – only very small percentage of diesel is necessary
Cheaper electricity production
Non-derated output power
The same response to load steps
High stability and increased protection of the engine
Lower emissions
Possibility of pure diesel operation maintained
Prolonged service intervals
Individual approach
Turn-key solution
Easy operation
Typical Convertable Engines
- Slow-speed (up to 750 rpm) turbocharged
- Middle-speed (around 1000 rpm) turbocharged
Book A Free Discovery Call
Unlock the potential of your power systems with a free discovery call at Applied Power Engineering.
Our expert team is eager to understand your unique challenges and goals, providing personalized insights and solutions tailored to your needs. This no-obligation consultation allows us to assess your requirements and explore how we can enhance your operations.
Take the first step towards optimised performance—schedule your free discovery call today!
From Our Blog
Stay up to date with what is new in our industry, learn more about the upcoming products and events.
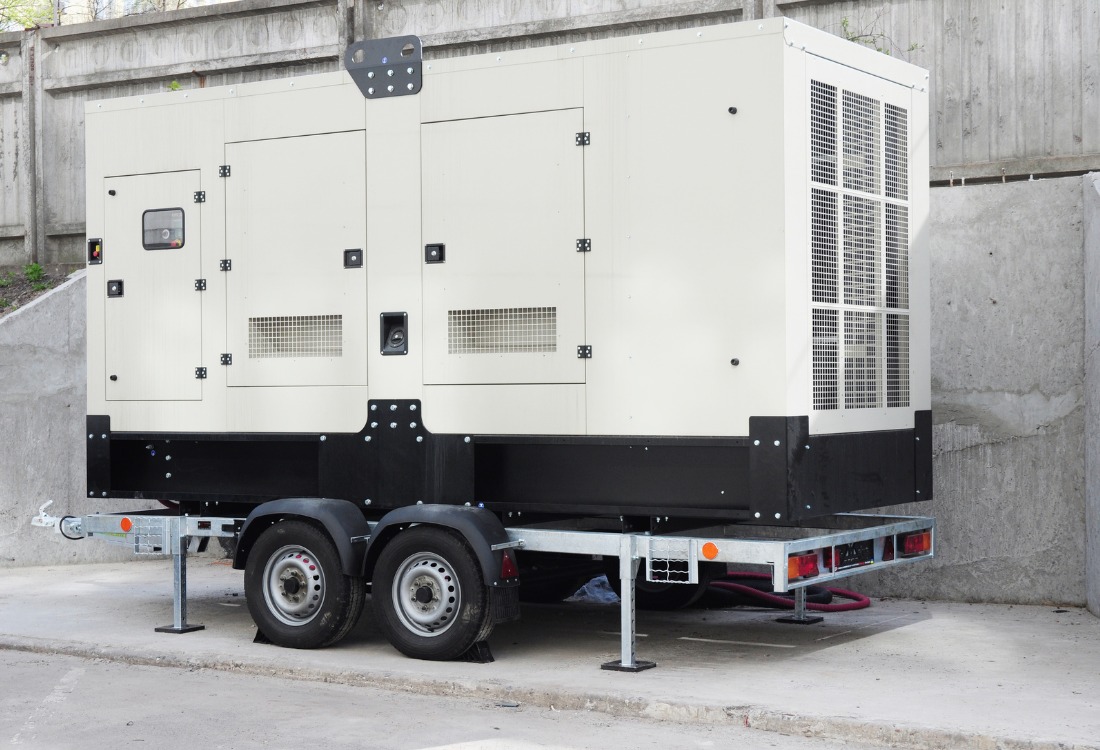
The Importance of Investing in Generators and Control Systems For Power Backup
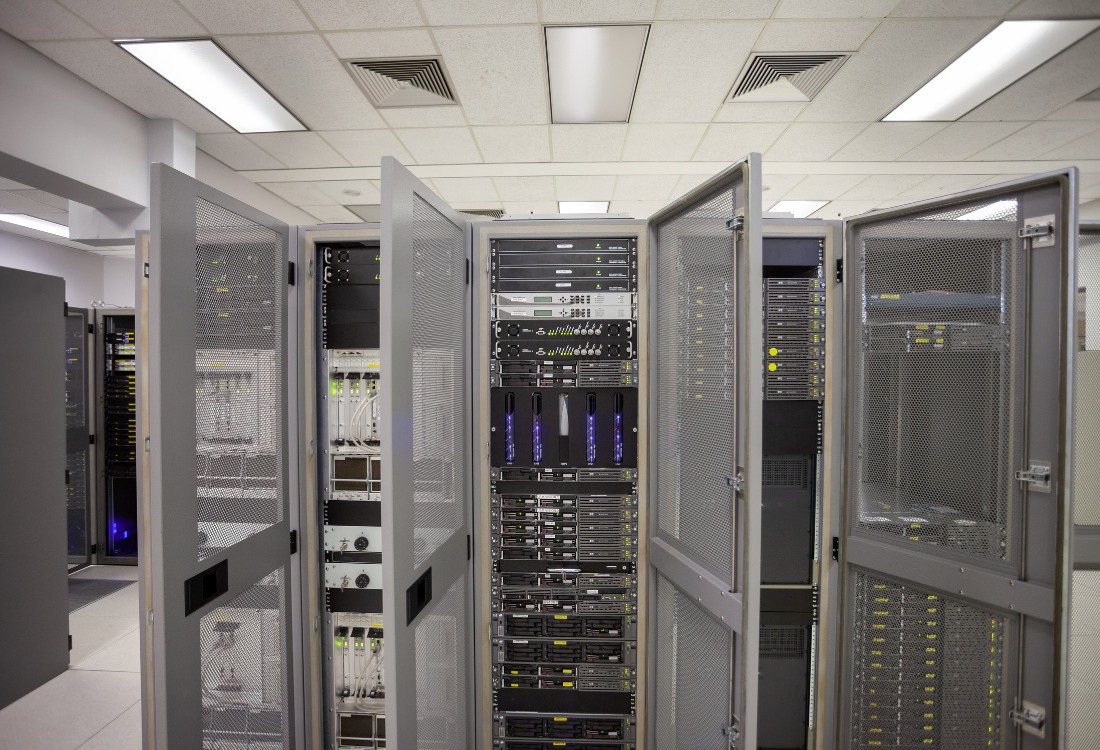
Why Backup Generators Are Essential For Data Centre Operations
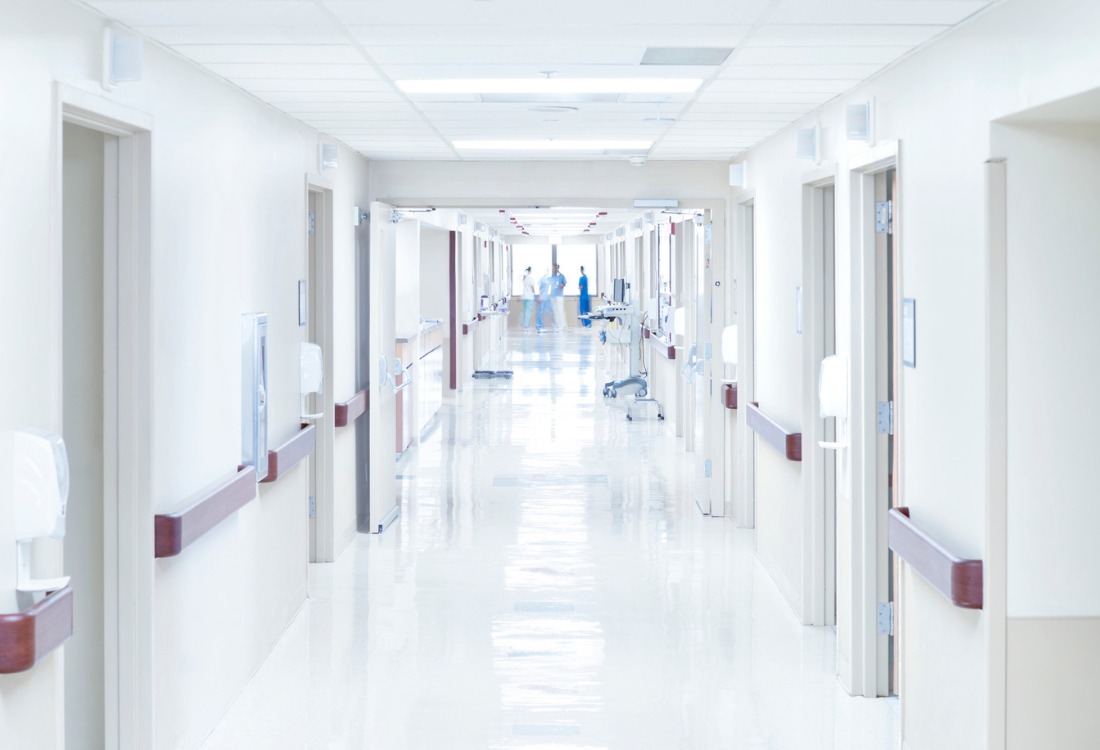